The Orthotics and Prosthetics department is exploring ways to incorporate digital technology into the design and production of orthotic and prosthetic solutions for clients. Digital technologies include scanners, design software, and 3D printers.
These innovative tools can be used at various points along the process and offers several benefits including:
- Reduced material waste
- Improved time efficiencies
- Improved ability to save, store, and replicate a device for a client
- Opportunities for innovative design features and materials
- Improved client experience
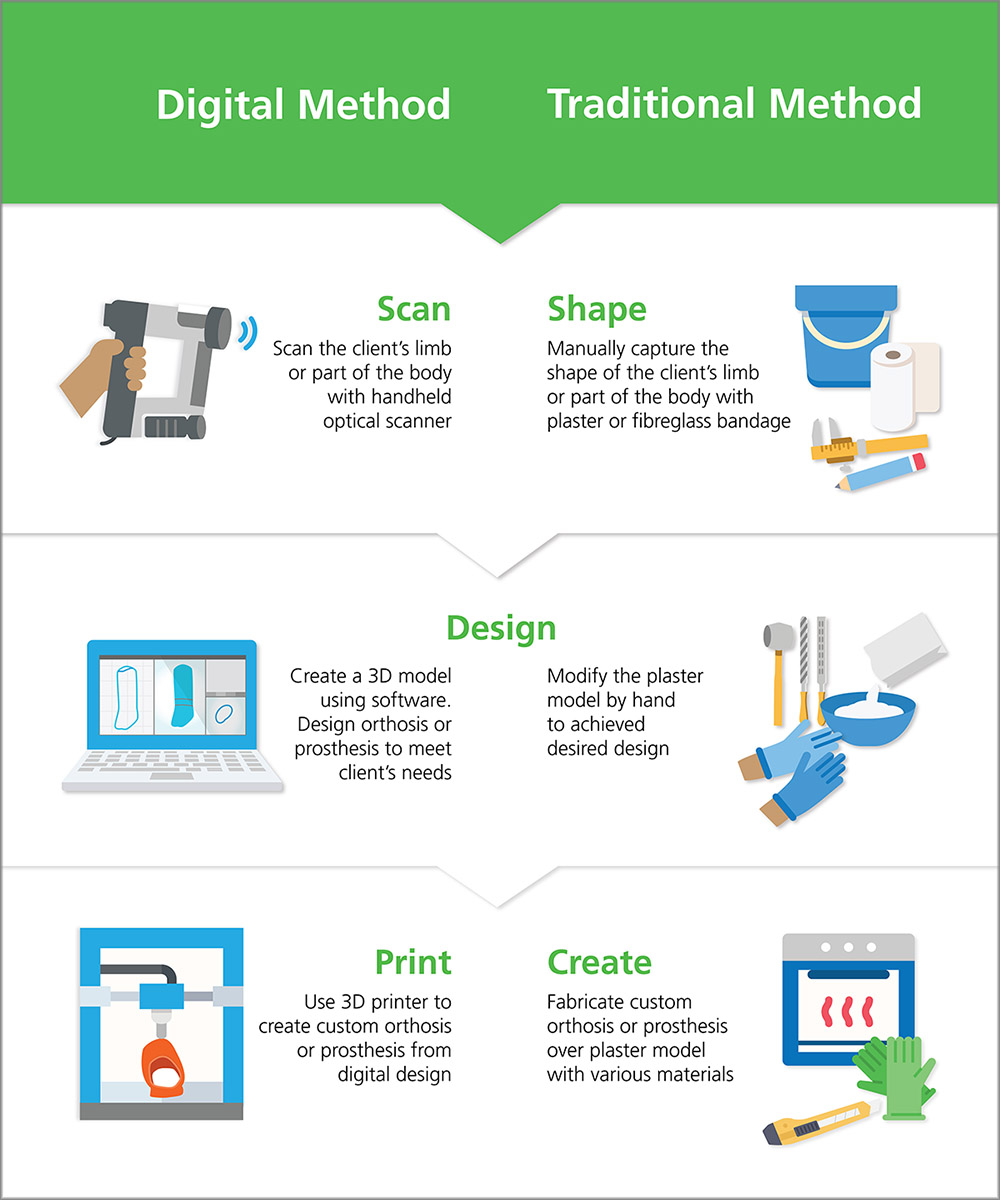
Digital Method
Scan - scan the clients limb or part of the body with handheld optical scanner
Design - create a 3D model using software. Design orthosis or prosthesis to meet client's needs
Print - use 3D printer to create custom orthosis or prosthesis from digital design
Traditional Method
Shape - manually capture the shape of the client's limb or part of the body with plaster or fibreglass bandage
Design - modify the plaster model by hand to achieved desired design
Create - fabricate custom orthosis or prosthesis over plaster model with various materials
Digital Technology Team
The Digital Technology team is comprised of clinicians from the Orthotics and Prosthetics department and researchers from the Bloorview Research Institute (BRI) PROPEL lab.
Collectively their aim is to investigate and develop evidence-based processes to bring digital technology into standard orthotic and prosthetic practice. As with all practices at Holland Bloorview, extensive and rigorous research is behind all newly implemented aspects of care to ensure it meets the standard of excellence that Holland Bloorview is known for.
Current Research and Clinical Projects
- Through a Centre for Leadership grant, our team is designing and 3D printing an adjustable forearm for clinicians to use to check the fit and function of a transradial socket
- This project is still in the research phase but will eventually be used with clients to optimize an upper limb prosthesis to best meet their needs
- Our team has invested in a digital scanner, design software and 3D printer to be able to 3D print transradial check sockets in-house
- This project is in the research phase and clients receiving a new transradial prosthesis may be asked to participate in a research study exploring the benefits and feasibility of 3D printed sockets
- Our team has partnered with Boundless Biomechanical Bracing to explore the benefits of scanning, designing and 3D printing AFOs
- This project is in the research phase and clients receiving a new AFO may be asked to participate in a research study exploring the benefits and feasibility of 3D printed orthoses
- Our team has developed a pathway to scan and design custom transtibial and transfemoral design liners
- By sending a digital file of the liner to the manufacturer, we can save on time and shipping costs
- This process is now in practice within the department